Cement History
Cement material in its current form and specifications is one of the leading discoveries that has made a fundamental change in the shape and style of buildings and construction. The cement industry has opened up broad horizons for the spread and development of the construction movement. World countries have rushed to build cement plants due to the importance of cement in building the national economy, as being the basic material necessary for building and construction works.
Kuwait has witnessed a period of wide-range urban and industrial activity, thus there was an imperative need to establish a cement industry on its lands. In the past, building was limited to mud, plaster, marine rocks, and wooden ceilings (Gandal, Bacillus, and papyrus(.Cement was not known to the people of Kuwait until 1912, and cement entered Kuwait for the first time when the American mission brought cement in barrels of wood to build the American hospital. Thereafter, the people of Kuwait realized the importance of this material in terms of hardness and strength. However, the use of cement continued to be limited due to its high price and unavailability, until Kuwait Cement Company was established in 1968, crowning a new era for the foundations of the comprehensive renaissance in the country.
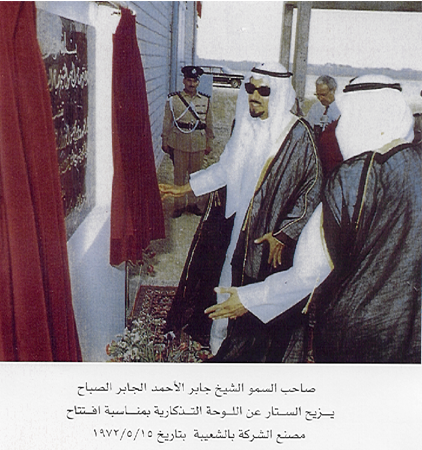
Ordinary Portland Cement (OPC Type 1):
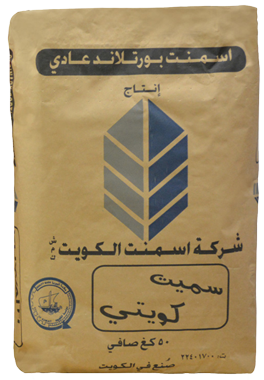
* Usage: This cement type is mostly used in construction works. It is used in concrete mixtures for casting ceilings, walls, concrete columns, and floors for buildings and installations. It is also used in the foam concrete mixtures, screed, and concrete mortar used in all finishing works such as interior and exterior paint and surveys, and also to fix the cement and lime blocks, Kashi, and curbstone tiles. It is also used in the manufacture of all types of cement products such as cement pipes, precast (readymade walls), cement and curbstone blocks, all types of tiles, and in the manufacture of adhesive materials used in construction.
* Characteristics: It achieves a high compression ratio compared to other types of cement, which makes it distinct when used in concrete works in general.
* Specifications: It is manufactured by the Kuwaiti standard specifications KSS 381-383 and the American standard specifications ASTM C 150.
Sulphate Resistant Cement Type V (SRC Type V):
* Usage: This cement has low C3A content to avoid sulfate attack from outside the concrete. This is the ideal cement when there is a need to resist sulphate salts and is most suitable for sub-surface structures like casting the bases and foundations for buildings that contain a large percentage of sulphate salts or structures used close to the marine environment.
* Characteristics: The ability to resist sulfate and chloride salts existing in the soil, which makes it distinct when used for concrete mixtures applied in installations located adjacent to the soil or in coastal areas.
* Specifications: It is manufactured by the Kuwaiti standard specifications KSS 381-383 and the American standard specifications ASTM C 150.
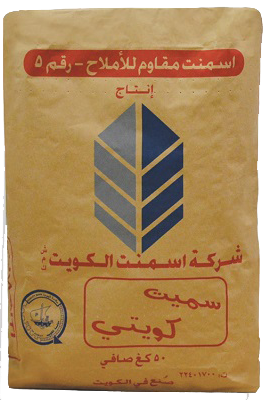
White Ordinary Portland Cement (WOPC Type 1):
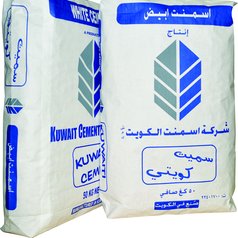
* Characteristics: It achieves a high compression ratio and an excellent degree of softness and whiteness, which gives aesthetic and artistic touches when used in decorations and finishing works.
* Specifications: It is manufactured by the Kuwaiti standard specifications KSS 381-383 and the American standard specifications ASTM C 150.
Oil Well Cement (OWC- Class G (HSR Grade)):
* Usage: Oil Well Cement is used exclusively in the wells for the production and exploration of oil and gas that are onshore or offshore in the deep sea water with a depth of 7000 feet (2100 meters). It is also used in damming and isolating water wells, waste disposal wells, and geothermal power wells. This type of cement has two functions:
- Protection of the well concealment from leaking liquids.
- Protection of the well concealment from rocks collapse.
There are various categories of Oil Well Cement: (A, B, C, D, H & G). The three cement categories mostly used in oil wells are A, G & H. Category A is used in most moderate wells and conditions less demanding, while categories G & H are used in wells that are the deepest, hottest, and highest in pressure.
Oil Well Cement is classified as follows: Ordinary (O), moderate sulfate resistant (MSR), and high sulfate resistant (HSR).
* Characteristics: Oil Well Cement is a high sulfate-resistant type, and is used in oil wells at the level of drilling depth. Resistance of sulfates depends on the Tricalcium Aluminates (C3A) content, which has an impact on the strength of cement hardness under the influence of sulfates.
Oil Well Cement is produced in conformity with the specifications of the American Petroleum Institute (API) and is characterized by quality, performance stability, and specifications.
Oil Well Cement has been designed very carefully due to its complex usage conditions in terms of temperature and pressure, hence meeting the requirements such as condensation time, high resistance to sulfates, high durability, low stable viscosity, low fluids, and strength.
* Specifications: Oil Well Cement is manufactured and tested by the American Petroleum Institute (API Spec 10A) for physical and chemical characteristics.
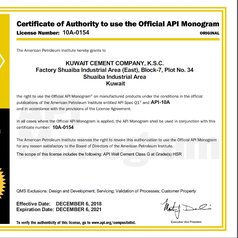
GGBS Material
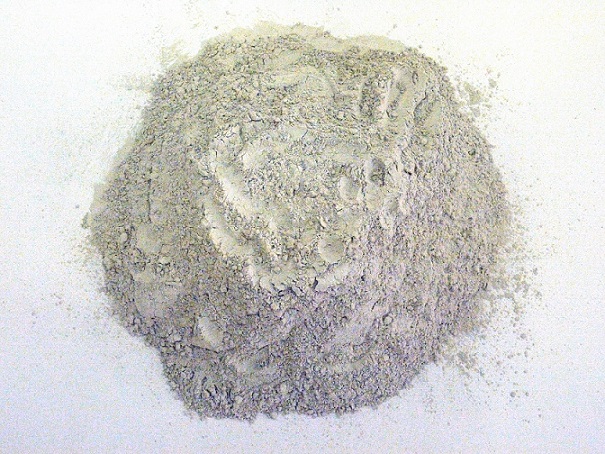
The GGBS material is a ground granulated blast furnace slag used directly by adding it to the components of concrete mixtures of Portland cement, or by mixing it in advance with cement to produce the Portland blast furnace slag cement. The slag cement has several grades of classifications which are determined based on the rations of mixing the GGBS with the ordinary cement.
* Usage: GGBS is used with the slag cement in all concrete mixtures used for bases, foundations, marine buildings, and those adjacent to the sea, large concrete block mixtures such as dams, bridges, roads, and prefabricated walls as well as concrete mixtures exposed to harsh environmental agents such as sewage and seawater, and concrete mixtures that require strength and high performance such as bridges and high-rise buildings.
* Characteristics: Usage of GGBS in concrete works adds better operational properties for the concrete mixture in terms of higher strength and hardness by achieving sufficient initial strength with high compression power. It also gives the concrete mixture high resistance to sulfate, chlorides, chemical corrosion, and corrosion of reinforced concrete, in addition to low-temperature hydration and low levels of overall alkaline reactions.
* Specifications: GGBS material is manufactured at the Company’s plant by the British standard specification BS EN 15167-1 and in conformity with the American standard specifications ASTM C989.